Today we're going to talk about diagrams. Sounds boring, I know, but I cannot stress enough how important this step is. I could just tell you how my diagram and all it's measurements turned out but I'm afraid that people won't go past it and customize their own door. Anyone who has diagrammed things out knows that it isn't terribly hard, it really isn't. It sounds a lot more intimidating than it really is. That's probably why so many people I talk to look at me like I have 6 heads when I talk about diagramming things out and then start telling me how smart I am which is just silly. Anyone can make a good diagram with a little practice. If you have no experience with a thing, of course it seems scary and anyone who can do this strange and wondrous thing must have some extra edge. Lies and propaganda, that is. Don't sell yourself short, you'd be surprised what you can pull of if you give it a shot. What it comes down to are skill sets, not intelligence, and you can't be good at something if you never try. Hence me taking you through the steps to make a diagram. Good diagrams will make your life sooo much easier, and not just for props. You can use them to lay out rooms without having to move your furniture (or appliances, if you're doing a kitchen) a gazillion times or use them to organize closets or design a planting plan for a garden. Diagrams are indispensable and it all comes down to one thing. Graph paper.
I adore graph paper and you should too. Sure, you could try to sketch out a grid on your own but unless you have a bunch of time and some seriously awesome drafting tools it isn't worth it. The grid is the most important part. All those evenly spaced lines are what let you make to-scale diagrams and I LOVE making to-scale diagrams! Yeah, I know. I'm odd. I blame my mother, she taught me how to do them when I was 12 so I could decide where my furniture went when we moved and I've been doing it ever since. You should see the one I made for the lab before we moved; it made the whole process super easy. Anyway, my door diagram made it possible to calculate how much foam board I would need, how many colors of paint, and what sort of bits needed to be cut out. All of that from one little sheet of graph paper.
For a good diagram you need to know the size object you're wanting to make and that means you need to know how much space you have where that object is going to go. For my diagram, I measured how wide my hallway is where I want the door to be and I measured how tall my doors are (standard doors in the USA are 80 inches tall, that's 6 feet 8 inches). I measured the doors instead of the height to the ceiling (which is also a standard measurement. Most residential ceilings are 8 feet high unless custom designed or vaulted) because I didn't want to have to make something that big. It would take more parts and be a lot harder to handle. You also want to take note of anything in the area that might cause problems. For instance, I have a built in linen closet where I want my door to go. It's mostly flat, but it has some molding at the top which sticks out about 2 inches from the wall and that has to be considered. For something like this you can usually get away with measuring things in 1/4 inch increments, the most precise I've ever been is 1/16ths of an inch. You generally don't need to be that specific for crafty/prop things; extreme detail is better for things like window treatment measurements, floor plans, and other big (and important) projects. Just make sure you measure everything the same way. Don't round up sometimes and round down others, pick a system and stick with it.
Right. So, I've measured my hall and found that my door has to fit in a space that is 34 inches wide and 80 inches tall. But, since 34 inches is the exact width of the hallway and there is no way I could get the door positioned well if it's the same size as the hall, the door will have to be slightly smaller. This is where some of the joys of graph paper come in. The graph paper I used has a 1/4 inch grid. That means there are 4 squares(in a row) to an inch. To make the scale convenient I made 1 inch equal 1 foot. In 12 inches there are 4 squares, 12 divided by 4 is 3 which makes each little block equal 3 inches in the real world. You'll want to mark your scale (how many inches you set each block to) on your paper so you don't forget. I've done that before and it's painful later. And now, some math. 34 is not evenly divisible by 3 (my scale measurement), but 33 is. I didn't just randomly pick 33 inches either. If my door is 33 inches wide it will fit the 34 inch space and it will be exactly 11 squares wide on the graph paper. 34 inches would have been 11 and 1/3 squares and that's just obnoxious to deal with especially if you don't have to. Same thing with the 80 inches high. It isn't easily divisible by 3, but 81 is. Since the door isn't going all the way to the ceiling it can be an inch higher than a door with no problems. Again, this is a prop and not a real door. You don't want to fudge a real door measurement like that but it's cool on a prop.
Having established that the door will be 33x81 that can be marked onto my grid (it comes out as 11 squares by 27 squares). Once the perimeters are marked you can start transferring your door idea (see The Door: Part 1) to the graph paper. The easiest patterns will have mostly straight lines, harder patterns will have curves. I'm lazy on top of being a bit of a perfectionist so I opted not to have any curves at all. Some of my pieces will need to be symmetrical and that is a lot easier to do with straight lines than curvy ones (I suck at free-handing symmetrical curves). It will make your life easier if you use the grid lines as much as possible. Try to use whole squares where ever possible, too. I tried not to cut grid squares into smaller than half to keep it easy.
I haven't mentioned something yet which is really super important for this project. Standard foam board, the kind you get at craft stores, is 20"x30" (in various thicknesses) and my door is 33"x81". You see where that might be a problem. 30x80 would be no problem; I would just stack 4 boards along their 30 inch edges and viola! 30x80. That is pretty much what I'm going to do, but to get the extra 3 inches side to side and the extra inch tall I have to be a little creative. On the diagram you can see that the door is bordered by a black and yellow band. That border is where my extra space is going to come from. Thick of it like a license plate and frame. The plate (door base) is a standard size but the frame (the black and white part on the door) can be any size at all so long as it covers a part of the plate. What you don't see on the diagram is that overlap. On my door it ends up being a 1 1/2 inch overhang on each side (1 1/2 + 1 1/2= 3, 3+30=33) and a half inch overhang on the top and bottom ( 1/2 + 1/2 = 1, 80 + 1 = 81). I know it helps if you can see what I'm talking about so I made a rough diagram in paint to demonstrate.
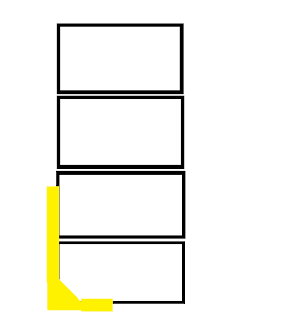
The rectangles represent the foam board base, the yellow is the foam board frame. Using overlapping pieces like that will get the extra few inches and help with the next issue.
After that pic, the other problem should be glaringly obvious. Seams. There will be seams where the foam board is butted together to form the base and the frame. Here's where it gets complicated. If the seams for the frame and the door line up it will wreck the stability of the door. You never want your weak points to line up like that. Happily, it's really easy to account for seams on your diagram. You already know that you can't have a piece that is more than 20 or 30 inches long, depending on the which side of the foam board you use, so you can sketch in where the seams would be. You'll have to think about how it will actually be put together to do that, but now is as good a time as any for that. You'd have to do it eventually anyway and it's better to do before you start cutting things out. You should end up with something like this:
The red arrows mark the seams in the door base. Notice how I've covered up as much of them as possible? That's to give the door extra stability. The door base pieces will be taped together on the back, but you can't do that on the front without it looking weird so instead you cover the seams with the decorative pieces. I actually tweaked the diagram a little to make sure I got maximum coverage. If you look you'll see little arrows on the piece shaped like an H and on the hexagon with the green center. That's to tell me to move those pieces upward so that the seam by the H gets covered.. The added stability is worth it and it makes the seams nice and discreet. I have also marked where the seams are for the frame, but they are really hard to see because the ends of the pieces follow the striping. I planned it that way to make the seams stand out less on the frame because there is no good way to cover them.
The other important thing to see on that diagram is that there are 4 seams on the door base, not the 3 you would get stacking 4 pieces of foam board. I had to shift the boards so that I can cut the place where the door opens. That's what the dark line between the middle two arrows is, the door opening. It isn't really going to open, but I have to make it look like it can or the effect is lost. To make it look good I didn't want any of that portion to be seamed which is why I had to shift the placement of the foam boards. One board will be cut into 2 pieces, it's the only good way to make it work.
Once you're happy with the seam placement and overall look for your door you can start figuring out the size of the decorative pieces. I did this by marking out one of each next to my door diagram and translating squares into inches. You only need 1 stencil per piece type which will make things go faster. My diagram has 6 red pieces on it, those are to be emergency door clamps, but they are all exactly the same size and shape so it would be silly to cut out 6 stencils when I only really need the 1. It will also make sure that the 'identical' pieces stay that way, which wouldn't happen if multiple stencils were made for the same piece.
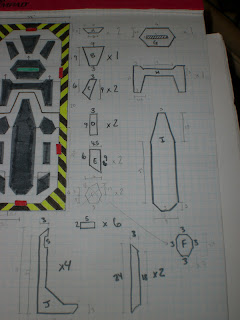 |
The two pieces on the bottom are the pieces for the frame. You can see the angled edges and the notches for the door clips in the piece labeled "J". That's how I'm going to fit it all together. |
Having the actual dimensions of the pieces is a handy thing for 2 reasons. It will help with the stencils and it's also how you figure out how much building material you need. I already know I need 4 sheets of foam board to make the door base, but how much do I need to the frame or the embellishment? Using my diagram I can calculate that I can only fit 2 of piece J onto a single board, so I need 2 boards for that. But I can get by with only those two boards for the frame because both of piece K (the long skinny one that I managed not to label) should be able to fit on one of the boards with the J pieces. So we're now +2 sheets of 1/2" foam board. If you want to get really fancy, you can make a diagram of how all your pieces need to be laid out. Using the graph paper you can fiddle with the layout until you have as few cuts and as little foam board as possible. Make sure you tape down your final layout so you don't forget where something goes and cost yourself extra material.
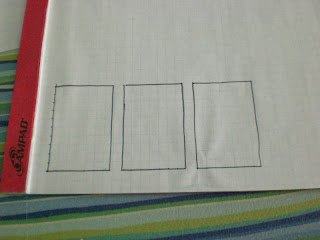
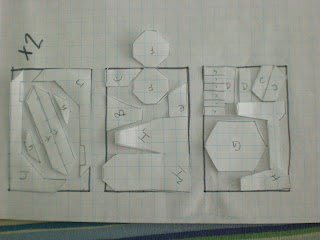 |
All my "pieces" laid out to get an idea of how much foamcore would be needed. The one piece that isn't in the line couldn't be made to fit but I didn't see the point of making another layout for a single piece. At least I'll have some extra board in the event I mess something up! |
All told I should need 7 sheets of 3/16" (4 for the door base and 3 for the cut outs) and 2 sheets of 1/2". You want to figure how much material you need before you start making stencils because you may find that you need to change something to fit your budget or supplies. If you can only afford 5 pieces of foam board and your project needs 15 it's better to find that out before you've started using your other materials.
And that, ladies and gentlemen, is why diagrams are awesome. Next up, stencils and construction!